Centrifugal pumps are important fluid transfer devices that are widely used to move liquids smoothly from one location to another. In this article, we take a deep dive into the product descriptions of centrifugal pumps, exploring their features, uses, and the ideal environment in which they excel. Whether you are a novice or an industry expert, this guide is designed to give you a thorough understanding of the basics of centrifugal pumps.
Centrifugal pumps consist of three main components: the motor, the impeller, and the pump body. When working, the motor drives the impeller to rotate rapidly, so that the liquid enters the pump body. The resulting centrifugal force pushes the liquid outward through the pump outlet. Centrifugal pumps are designed with various structures and materials to meet different application scenarios and ensure the best performance and durability.
Advantages and Features:
Centrifugal pumps have several key advantages that make them the first choice in various industries. First, they are designed to be simple and easy to install, allowing them to be quickly integrated into existing plumbing systems. Additionally, these pumps have high efficiency, allowing them to transfer fluids quickly and efficiently with minimal energy consumption. Centrifugal pumps are able to handle a wide range of fluid viscosities and temperatures, and thus are able to handle different liquids in different environments.
Additionally, centrifugal pumps are available in a variety of materials to suit specific applications. Pumps made of stainless steel are highly resistant to chemicals, high temperature and high pressure conditions. On the other hand, pumps made of lightweight materials like plastic facilitate installation and transportation.
how to use:
Operating a centrifugal pump is relatively simple. First, it is critical to ensure that the pump is properly installed and precisely connected to the piping system. This includes properly aligning the pump with the connecting tubing and ensuring a tight seal to prevent any leaks. Once the pump is in place, power should be connected and the motor started. Pump performance must be monitored regularly, paying attention to pressure and flow to ensure optimum efficiency.
Ideal environment:
Centrifugal pumps are widely used in various industries due to their adaptability to different environments. In the chemical industry, pumps made of materials such as stainless steel are critical to the safe transfer of harsh chemicals. These pumps can withstand corrosive substances and remain functional even under chemically aggressive conditions.
In high temperature applications, centrifugal pumps with advanced cooling systems and heat-resistant materials can effectively handle high temperatures without compromising performance. Additionally, the lightweight and portable nature of plastic centrifugal pumps make them suitable for applications that require quick installation and transportation, such as construction sites or agricultural settings.
in conclusion:
In conclusion, understanding the basics of centrifugal pumps is essential for both novices and industry professionals alike. Their efficient fluid transfer capabilities, wide choice of materials, and adaptability to different environments make them indispensable tools in various industries. Whether transferring liquids in chemical plants, handling temperature-sensitive substances, or facilitating construction projects, centrifugal pumps have always proven their worth. By providing a comprehensive product description, this article aims to provide the reader with the knowledge necessary to make an informed decision when selecting and using a centrifugal pump.
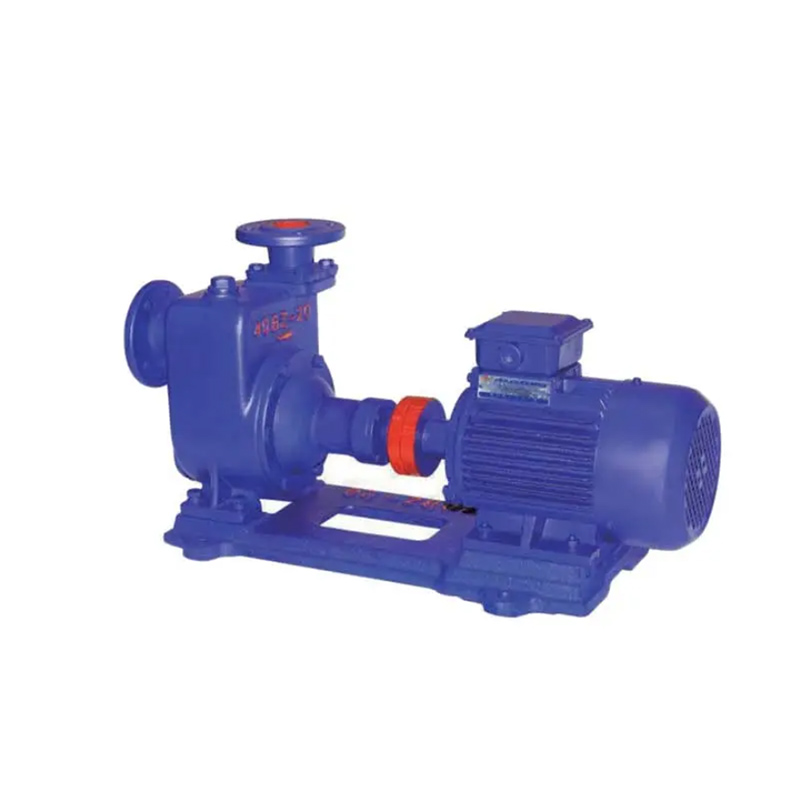
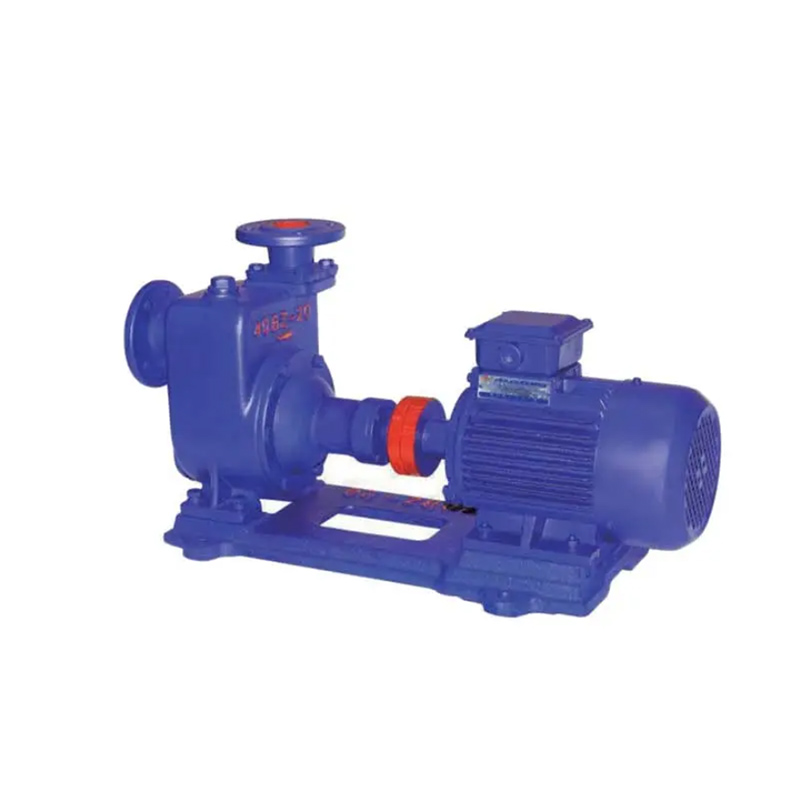
Post time: Aug-09-2023